Tech to the Rescue: IT Consolidation in Manufacturing
Bridging the Manufacturing Labor Gap: The IT Revolution
Last updated:

Edited By
Mackenzie Ferguson
AI Tools Researcher & Implementation Consultant
The manufacturing sector faces a looming workforce crisis, with a projected 1.9 million unfilled jobs by 2033. To combat this, companies are turning to IT consolidation as a solution. This strategy leverages work-management platforms to enhance productivity, streamline information access, and improve employee retention. With a focus on centralizing data access and maintaining valuable legacy systems, manufacturers are poised to significantly mitigate the effects of labor shortages.
The Emerging Labor Shortage in Manufacturing
The manufacturing sector is experiencing a significant labor shortage, with an estimated 1.9 million positions projected to remain unfilled by 2033. This shortage is primarily driven by an aging workforce that is retiring at a rapid pace, compounded by a lack of interest from the younger generation due to misconceptions about the industry's reliance on automation. As the sector is only in the early stages of digital transformation, there are untapped opportunities to attract new talent and improve workforce engagement.
One proposed solution to this labor gap is through IT consolidation, which seeks to increase productivity and efficiency by implementing unified work-management platforms. These platforms can facilitate better knowledge transfer, enhance employee retention, and streamline access to information, thereby reducing the time spent on reporting. Consolidation efforts are not aimed at eliminating existing systems but rather focus on integration to maintain cost-effective tools and enhance accessibility without redundancy.
Learn to use AI like a Pro
Get the latest AI workflows to boost your productivity and business performance, delivered weekly by expert consultants. Enjoy step-by-step guides, weekly Q&A sessions, and full access to our AI workflow archive.
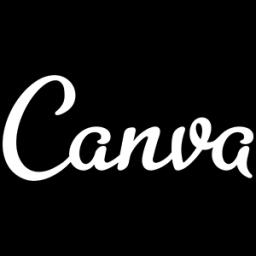
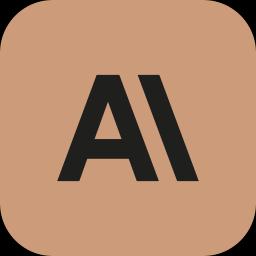
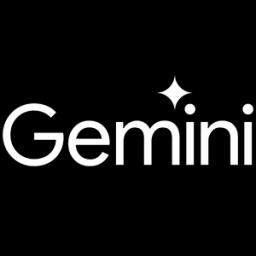
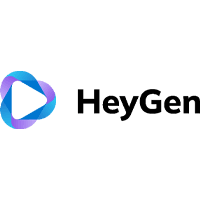
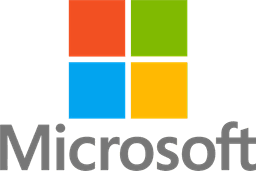
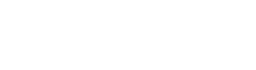
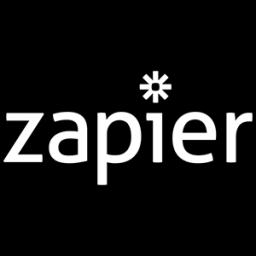
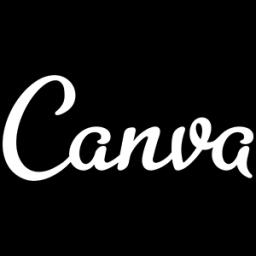
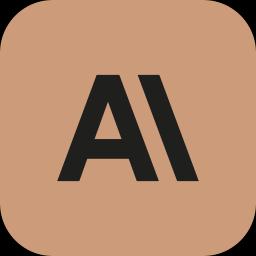
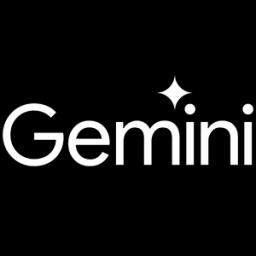
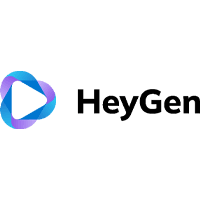
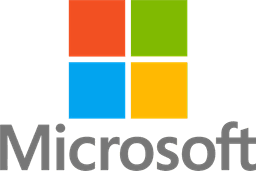
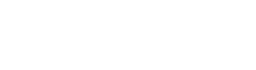
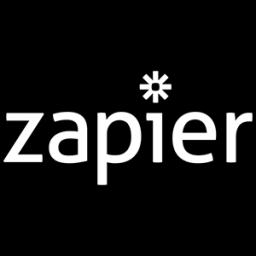
To address the shortages immediately, many manufacturers are taking proactive steps such as offering higher wages to attract skilled workers. Additionally, 57% of these companies are already adopting IT consolidation strategies to counteract the inefficiencies caused by information silos and outdated processes. By streamlining operations and improving training efficiency, manufacturers aim to preserve valuable legacy systems while meeting the demands of modern manufacturing environments.
IT Consolidation as a Solution to Workforce Issues
The manufacturing industry is grappling with a significant labor shortage, with predictions indicating that there will be around 1.9 million unfilled jobs by 2033. This problem is exacerbated by an aging workforce retiring in droves, while many younger individuals shy away from manufacturing careers due to misconceptions about automation and a lack of digital transformation. The industry's slow pace in embracing digital technologies has both contributed to the labor gap and offers a ray of hope in its capacity to attract new talent through modernization efforts.
IT consolidation emerges as a viable solution to the manufacturing sector's labor problems. By integrating work-management platforms, organizations can significantly improve productivity and efficiency. This technological advancement enables easier transfer of knowledge and retention of employees by providing streamlined access to information, thus diminishing the time and resources spent on reporting. It also helps in maintaining the invaluable legacy systems already in place while pushing modern IT solutions to the fore.
To tackle the immediate challenges, manufacturers are not solely relying on raising wages to attract skilled workers. Many companies are simultaneously implementing strategies around IT consolidation. About 57% of manufacturers are already increasing wages alongside deploying IT solutions to address workforce issues. This dual approach not just incentivizes workers financially but also optimizes the workplace environment, making it more attractive and efficient for existing and potential employees.
Learn to use AI like a Pro
Get the latest AI workflows to boost your productivity and business performance, delivered weekly by expert consultants. Enjoy step-by-step guides, weekly Q&A sessions, and full access to our AI workflow archive.
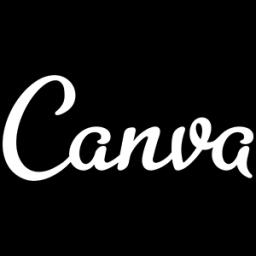
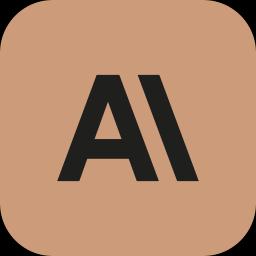
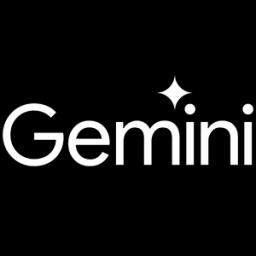
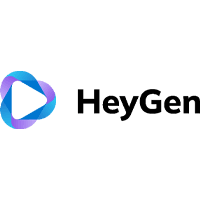
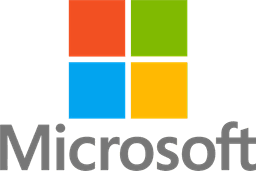
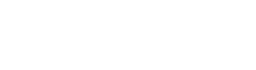
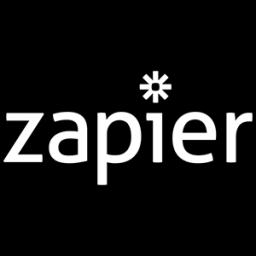
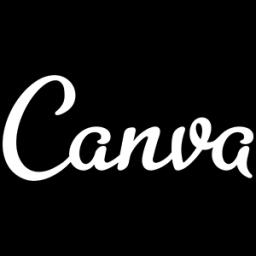
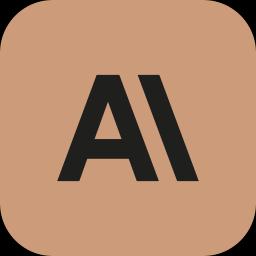
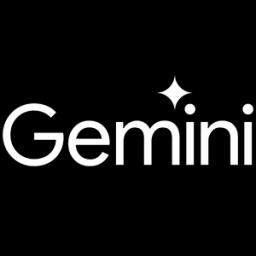
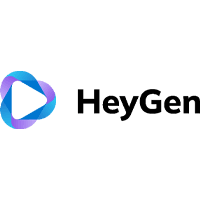
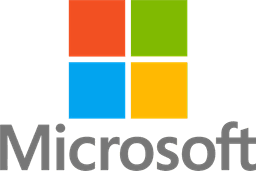
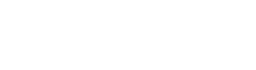
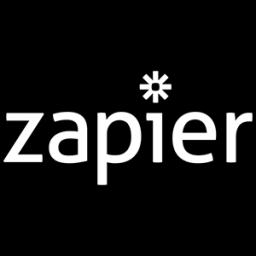
The fear of existing systems being completely replaced is unfounded as the focus shifts more towards integrating and streamlining current systems rather than eliminating them. The aim is to preserve cost-effective tools that have proven their worth over time while simultaneously improving overall accessibility and functionality. This method ensures that knowledge and traditional practices remain intact even as new digital pathways for work are created.
The role of IT consolidation in workforce development is noteworthy, particularly for its potential to ease the training processes and improve the transfer of knowledge. Centralized platforms can simplify the onboarding of less-skilled workers who require substantial on-the-job training. This aspect is crucial in upskilling a new generation of workers who can adapt to both traditional manufacturing roles and new hybrid roles that demand technical prowess.
Facing severe skill gaps, the manufacturing industry is not only adapting through IT strategies but is actively participating in campaigns aimed at encouraging younger generations to join the sector. Efforts like "Make Your Future," supported by major manufacturers, and educational collaborations highlight a shift towards making manufacturing jobs more appealing for the youth. Moreover, the emphasis on creating standardized training programs reflects the industry's commitment to a more skilled and versatile future workforce.
In conclusion, the move towards IT consolidation in the manufacturing sector is a pivotal step toward overcoming workforce challenges. By enhancing productivity, simplifying systems, and improving knowledge transfer, companies can not only fill the labor shortages they are currently facing but can also pave the way for a more efficient and digitally adept workforce. The integration of IT systems does not just bridge the gap left by an aging workforce but also attracts new, technology-savvy individuals eager to contribute to a revitalized industry.
Understanding the Role of Automation and Digital Transformation
The manufacturing industry is at a pivotal juncture where automation and digital transformation are not just enhancing operations but are essential survival tools in the face of labor shortages. As manufacturers grapple with a projected shortfall of 1.9 million workers by 2033, leveraging technology becomes a strategic imperative. Automation lowers dependency on manual labor, facilitates efficient knowledge transfer, and aids employee retention by eliminating repetitive tasks, thereby creating a more engaging workplace.
Digital transformation is paving the way for integrated work-management platforms. These platforms consolidate IT processes, providing a seamless flow of information across various functions. They allow for quicker report generation and enhance training processes, which are vital as companies strive to onboard and upskill a new generation of workers, many of whom are hesitant or unfamiliar with the manufacturing environment. Furthermore, digital tools enhance legacy systems, ensuring valuable processes are preserved while simultaneously streamlining operations.
Learn to use AI like a Pro
Get the latest AI workflows to boost your productivity and business performance, delivered weekly by expert consultants. Enjoy step-by-step guides, weekly Q&A sessions, and full access to our AI workflow archive.
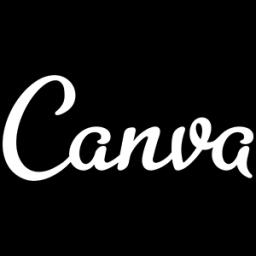
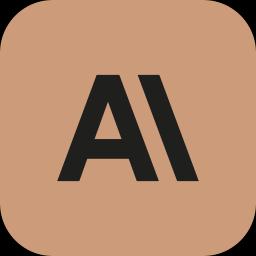
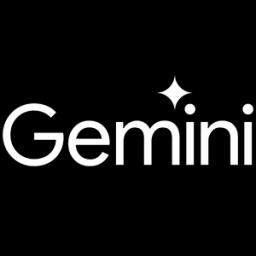
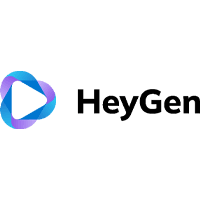
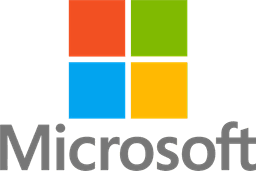
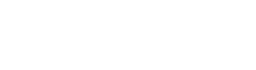
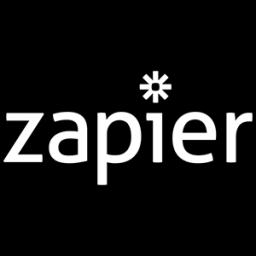
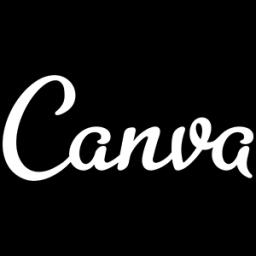
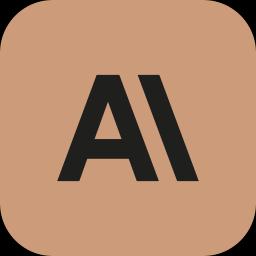
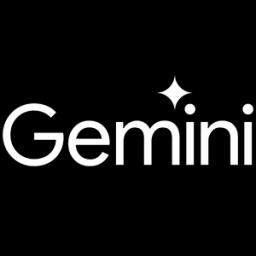
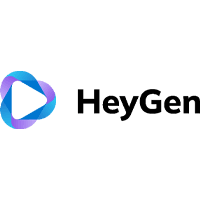
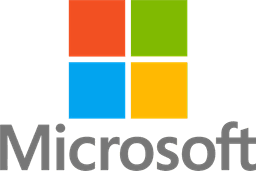
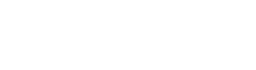
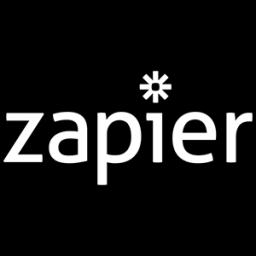
The labor gap in manufacturing has been compounded by a retiring workforce and the younger generation’s skepticism towards industry roles, largely influenced by misconceptions around automation. Contrary to the belief that technology displaces jobs, it actually fosters opportunities for skilled work within automated and semi-automated environments. Thus, educating potential workers on the benefits of technology in manufacturing is crucial to attracting talent.
Experts advocate that IT consolidation is more than just a stop-gap solution for current labor shortages; it's a redesign of the manufacturing workforce landscape. By integrating essential digital tools, companies can unlock new operational efficiencies and better manage skilled labor scarcity. In a competitive labor market, manufacturers adopting such strategies not only future-proof their operations but also make themselves more attractive to a digitally literate workforce.
Common Misconceptions and Challenges
The manufacturing sector is currently embroiled in a dual battle of misconceptions and challenges that jeopardize its growth trajectory. Despite technological advancements, there's a widespread notion that automation and AI are rendering manufacturing jobs obsolete, which dissuades younger generations from pursuing careers in this sector. This misconception is coupled with an ongoing labor shortage, predicted to leave 1.9 million positions unfilled by 2033.
One of the principal misconceptions plaguing the manufacturing industry is that technology will entirely replace human jobs when, in reality, it is reshaping roles to include more technical and digital skills. The early stages of digital transformation in manufacturing present an opportunity to dispel these myths by showcasing how technology can augment human capabilities, improve productivity, and create more engaging career paths.
Challenges in addressing these misconceptions are amplified by barriers such as information silos and outdated processes that hinder productivity. The industry's hesitance to fully embrace IT consolidation due to fears of disrupting legacy systems further exacerbates these issues. Yet, IT consolidation is a pivotal strategy that offers a coherent framework for improving efficiency, information accessibility, and maintaining longstanding systems, aiding in the reshaping of public perceptions around modern manufacturing roles.
Additionally, immediate challenges include competitive wage pressures, where merely increasing pay does not suffice to attract the required talent. Instead, a blend of strategies involving IT integration, streamlined processes, and enhanced training programs is urgently needed. These approaches not only retain valuable employees but also attract a more diverse and skilled workforce, aligning with the sector's evolving needs and dispelling the misconception of manufacturing as an outdated or declining career path.
Learn to use AI like a Pro
Get the latest AI workflows to boost your productivity and business performance, delivered weekly by expert consultants. Enjoy step-by-step guides, weekly Q&A sessions, and full access to our AI workflow archive.
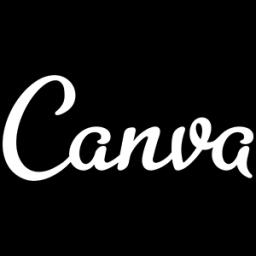
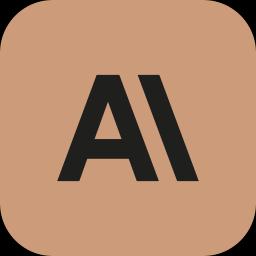
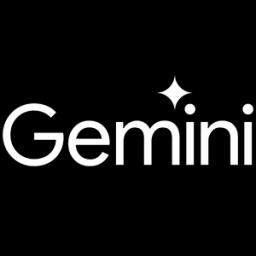
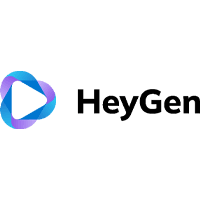
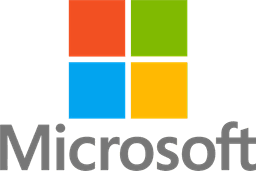
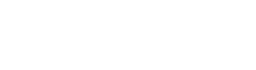
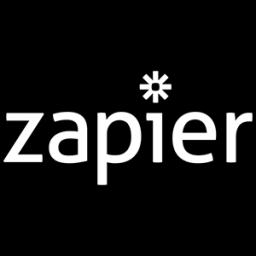
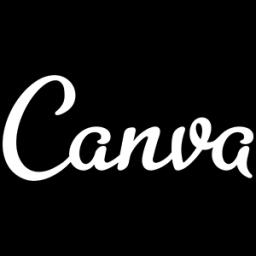
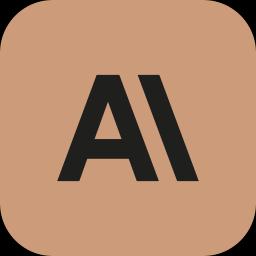
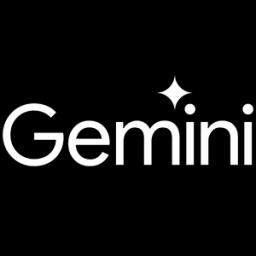
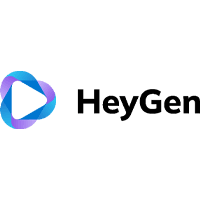
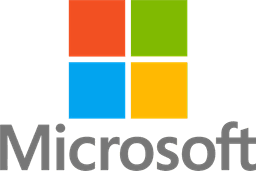
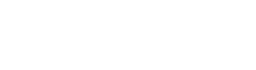
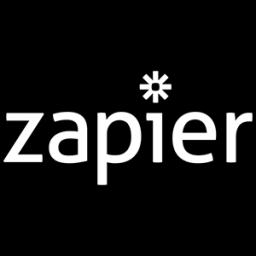
Moreover, the misconception that existing systems in manufacturing will be rendered obsolete is a misnomer. Instead, the focus is on integration and enhancement of existing frameworks, which promises to streamline operations without necessitating the abandonment of cost-effective tools. By promoting a narrative of enhancement rather than replacement, manufacturers can correct these misconceptions while addressing the real, tangible challenges that confront the industry today.
Immediate Actions Taken by Manufacturers
Amidst a critical labor shortage, with projections indicating up to 1.9 million unfilled positions by 2033, manufacturers are taking immediate action to address the gap. A primary strategy involves IT consolidation, utilizing work-management platforms to enhance productivity, streamline information access, and bolster employee retention. By improving these operational aspects, manufacturers aim to optimize their existing workforce, ultimately reducing dependency on manual labor and accelerating the onboarding of less-skilled workers.
IT consolidation not only aids in overcoming immediate workforce hurdles but also preserves valuable legacy systems. This approach focuses on streamlining and integrating existing resources rather than eliminating them. In addition to updating tech infrastructure, 57% of manufacturers have increased wages to attract skilled workers. These efforts are focused on short-term retention and attraction of talent while building a foundation for more sustainable future growth.
For workforce development, centralized platforms simplify processes like training and knowledge transfer. This is crucial for onboarding less-skilled workers who require significant on-the-job training. The standardization of training programs and collaboration with technical schools are part of a broader effort to bridge the skills gap, as seen in partnerships spearheaded by organizations like the National Association of Manufacturers.
Furthermore, manufacturers are aligning with industry-wide initiatives that standardize training and certification pathways, enabling better knowledge transfer and equipping the workforce with vital skills for modern manufacturing. Expert opinions emphasize the need for broadening talent pools and investing in both technological upgrades and human capital as part of cohesive long-term strategies for overcoming the manufacturing sector's labor challenges.
Case Studies and Related Events
The manufacturing industry is currently facing a significant labor shortage, with a projected 1.9 million unfilled jobs by 2033. This shortage is primarily driven by the retiring workforce and younger generations' hesitancy towards the industry due to misconceptions about automation. To tackle this issue, IT consolidation has been proposed as a solution to improve productivity, streamline knowledge transfer, and enhance employee retention by enabling better access to information and reducing time spent on reporting tasks. These strategies are seen as vital steps towards closing the labor gap in the manufacturing sector.
Learn to use AI like a Pro
Get the latest AI workflows to boost your productivity and business performance, delivered weekly by expert consultants. Enjoy step-by-step guides, weekly Q&A sessions, and full access to our AI workflow archive.
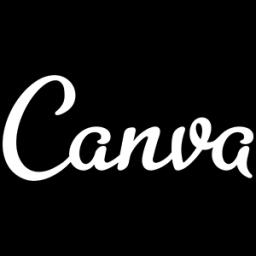
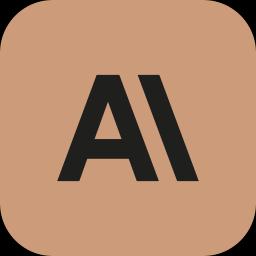
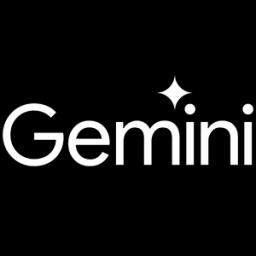
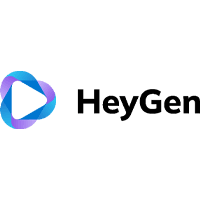
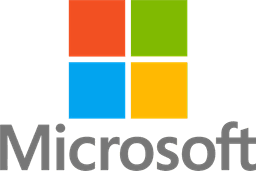
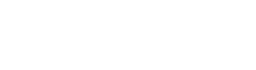
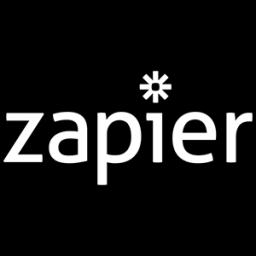
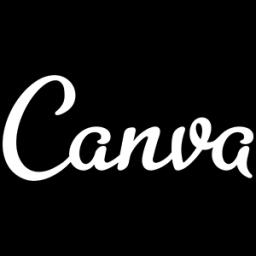
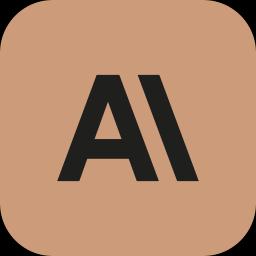
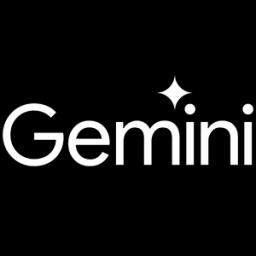
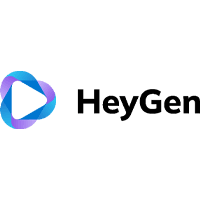
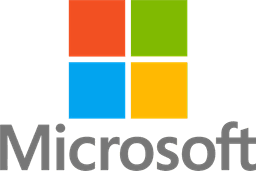
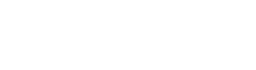
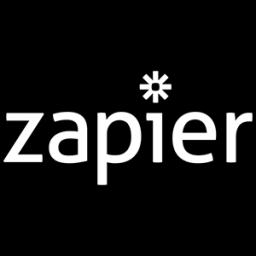
In response to the labor crisis, manufacturers are taking several actions including increasing wages to attract skilled workers. While a majority are investing in IT consolidation strategies, the goal is not to eliminate existing systems but to integrate and streamline them. This approach is designed to maintain cost-effective legacy systems while improving accessibility and creating unified information access, which significantly reduces the time needed for generating reports and improves training efficiency.
Recent developments in the industry underscore the urgency of addressing the labor shortage. For instance, major automakers such as Ford and GM have reported significant workforce gaps affecting production schedules. In response, initiatives like the "Make Your Future" campaign by the National Association of Manufacturers aim to attract younger workers to manufacturing careers. Moreover, a record high of manufacturing job openings and accelerated retirement rates as reported by the Bureau of Labor Statistics highlight the pressing need for workforce development.
Experts have weighed in on the crisis with varying perspectives. Carolyn Lee of the Manufacturing Institute highlights the importance of diversifying the talent pool by tapping into underrepresented groups such as returning mothers and refugees. Meanwhile, Josh Cranfill from Quickbase emphasizes the role of IT consolidation in overcoming productivity barriers caused by information silos. Additionally, the Deloitte Research Team points out the need for technical worker training and suggests augmenting the workforce with AI and digital tools.
The implications of the manufacturing labor shortage extend beyond immediate workforce challenges, predicting a future economic impact with potential GDP declines, increased consumer prices, and a slowdown in reshoring efforts. To mitigate these, the industry is expected to adopt automation and AI technologies rapidly. Moreover, workforce transformation will move towards hybrid roles requiring both technical and digital skills, necessitating enhanced investment in workforce development and adaptation of higher education programs. The industry is also likely to see a restructuring with smaller manufacturers consolidating and a shift towards manufacturing-as-a-service models.
Expert Opinions on Bridging the Labor Gap
The manufacturing sector is experiencing a significant labor shortage, with an alarming projection of 1.9 million unfilled jobs by 2033. This shortage is driven by a retiring workforce, misconceptions about automation among younger generations, and an industry still in the initial stages of digital transformation. Despite these challenges, there is a silver lining, as the crisis also presents an opportunity for innovation and transformation within the sector.
One of the proposed solutions to bridge this labor gap is through IT consolidation. By implementing comprehensive work-management platforms, manufacturers can increase productivity and efficiency, improve knowledge transfer, and enhance employee retention. These platforms also streamline information access, significantly reducing the time spent on reporting, and maintaining the functionality of valuable legacy systems while integrating new technologies.
Learn to use AI like a Pro
Get the latest AI workflows to boost your productivity and business performance, delivered weekly by expert consultants. Enjoy step-by-step guides, weekly Q&A sessions, and full access to our AI workflow archive.
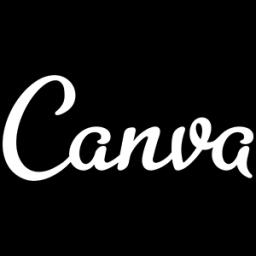
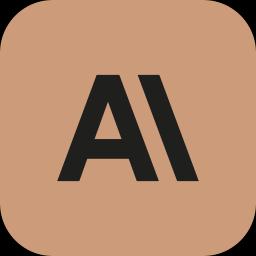
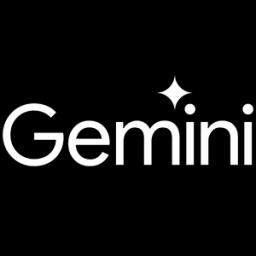
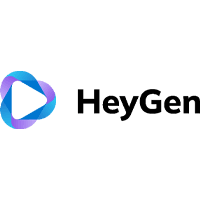
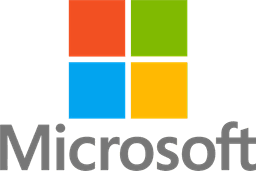
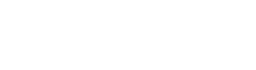
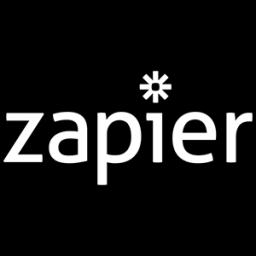
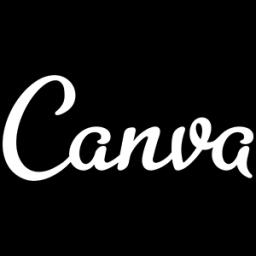
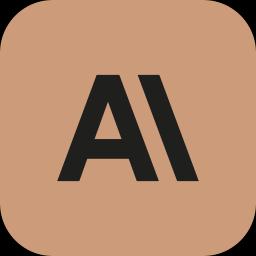
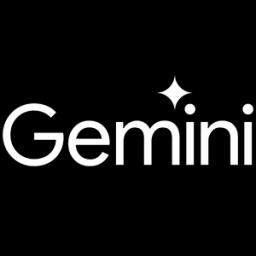
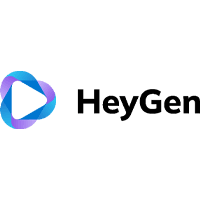
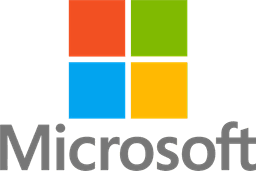
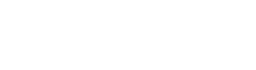
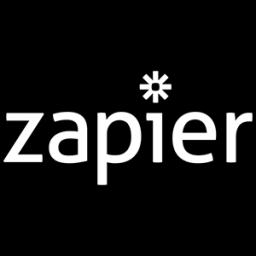
Currently, many manufacturers are stepping up efforts to attract skilled workers by increasing wages and simultaneously implementing IT consolidation strategies. About 57% of manufacturers are pursuing this dual approach as an immediate response to the labor crisis. However, experts like Josh Cranfill emphasize that wage hikes alone are insufficient. Overcoming information silos and outdated processes through IT improvements is critical to boosting productivity and unlocking potential efficiencies in the workforce.
Consolidation and modernization of IT systems help streamline manufacturing processes without eliminating existing systems. Instead, the focus is on enhancing accessibility and ensuring seamless integration, which supports training efforts and expedites knowledge transfer. This is particularly crucial for onboarding workers who may possess less technical expertise, allowing for effective on-the-job training and development in line with modern manufacturing needs.
In response to the labor shortage, several related events have unfolded, highlighting both challenges and initiatives aimed at addressing the issue. Major automakers, like Ford and GM, face significant production delays due to a 20% gap in skilled workers within their manufacturing facilities. Meanwhile, the National Association of Manufacturers has launched a $10 million "Make Your Future" campaign to attract younger workers, alongside partnerships with technical schools across multiple states.
Furthermore, a record number of manufacturing job openings, reaching 1.2 million positions, have been recorded, exacerbated by a faster-than-expected retirement rate. To counteract this, leading manufacturers such as Siemens, Honeywell, and Johnson Controls have joined forces to establish standardized training programs and certification pathways, aiming to equip new workers with modern manufacturing skills essential for today’s workforce.
Future Economic and Workforce Implications
The current and upcoming economic landscape is heavily influenced by the evolving dynamics within the manufacturing sector, particularly in response to a persistent labor shortage. With projections pointing to approximately 1.9 million unfilled positions by 2033, economic activities tied to manufacturing might face significant headwinds. The reliance on traditional labor could sharply decline as industries increasingly adopt automation and AI technologies. Such technological shifts are seen not only as a necessity to bridge the labor gap but also as a catalyst for new economic opportunities, albeit compounded by rising consumer prices due to heightened labor and production costs. Moreover, this scenario implies potential slowdowns in reshoring efforts, as companies may grapple with staffing challenges at domestic facilities. This introduces complexities in global supply chain management, as firms strive to balance efficiency with capacity constraints.
On the workforce development front, there is an anticipated transformation emphasizing the need for hybrid manufacturing roles that combine technical and digital skills. Companies are likely to intensify their focus on workforce development initiatives and technical education to keep pace with these changes. An inclusive approach towards labor market participation is expected to emerge, drawing from alternative labor pools such as returning workers and underrepresented groups. This shift will necessitate new compensation models centered around skills, offering incentives for performance-driven contributions.
Learn to use AI like a Pro
Get the latest AI workflows to boost your productivity and business performance, delivered weekly by expert consultants. Enjoy step-by-step guides, weekly Q&A sessions, and full access to our AI workflow archive.
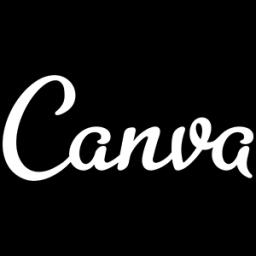
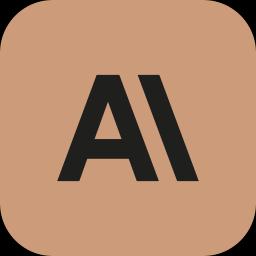
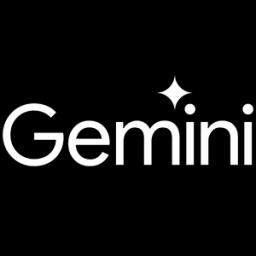
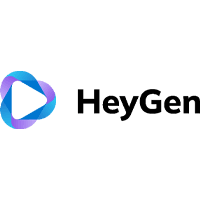
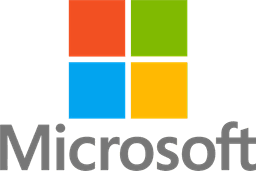
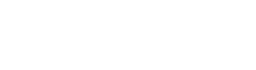
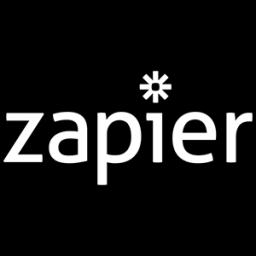
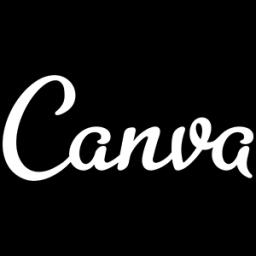
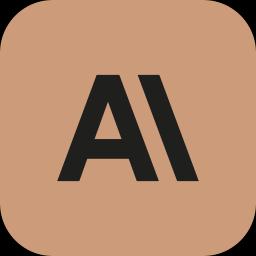
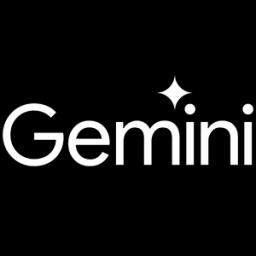
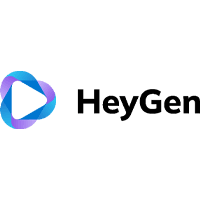
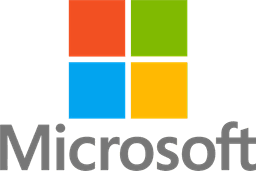
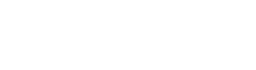
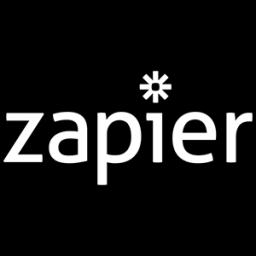
The industry structure is poised to experience consolidation, particularly among smaller manufacturers unable to secure or retain limited talent. This trend may accelerate the adoption of manufacturing-as-a-service models, underpinned by a strong emphasis on IT integration and broad digital transformation across sectors. Collaborative efforts, such as the development of standardized industry-wide training and certification programs, will likely gain traction, assisting in closing skills gaps while fostering uniformity in capabilities amongst the workforce.
From a policy perspective, the implications are substantial. There is likely to be increased advocacy for immigration reforms to help bridge the skilled labor shortage, alongside calls for enhanced funding for manufacturing education and training programs. New regulatory frameworks may be instituted to govern the integration of automation and AI within manufacturing environments. Furthermore, governments might consider offering tax incentives to companies investing significantly in workforce development initiatives, encouraging continued investment in human resources alongside technological advancements.
Strategizing for the Future: Industry and Policy Recommendations
The manufacturing industry is facing unprecedented challenges, driven primarily by a significant labor shortage projected to leave 1.9 million jobs unfilled by 2033. This situation threatens not only the productivity of individual businesses but the entire sector's contribution to the economy. As the industry grapples with an aging workforce, it is imperative for both industry leaders and policymakers to develop comprehensive strategies to address these challenges. This section will outline recommendations for both manufacturers and policymakers, focusing on the potential for IT consolidation, workforce development, and policy reforms.
To address the looming labor shortage, manufacturing companies must prioritize IT consolidation and the adoption of unified work-management platforms. This technological advancement can significantly enhance productivity and efficiency by streamlining access to information and reducing the time spent on mundane tasks like report generation. Additionally, such platforms promote better knowledge transfer and employee retention by improving training processes and simplifying onboarding for new workers. By maintaining existing valuable systems and integrating new IT solutions, manufacturers can create a more adaptable and robust operational environment.
For effective workforce development, it is critical for manufacturers to invest in training and education programs that align with modern manufacturing demands. Collaborations between industry leaders and educational institutions can lead to the creation of standardized training and certification programs that not only attract new workers but also upskill existing ones. This will ensure that the workforce is equipped with the necessary skills to thrive in a digitally transforming industry. Furthermore, manufacturers should explore innovative compensation models that go beyond wage increases, incorporating performance incentives and skills-based pay to attract and retain talent.
Policymakers, on the other hand, play a crucial role in creating an enabling environment for these strategic shifts. There is an urgent need for immigration reform to introduce more skilled labor into the manufacturing sector. Additionally, increased government investment in education and training programs is essential to cultivating a future-ready workforce. By providing tax incentives for companies that invest in workforce development and encouraging research into AI and automation, legislators can bolster the industry's resilience against labor shortages. New regulations should also be crafted to ensure the ethical and effective implementation of technology in manufacturing processes.
Learn to use AI like a Pro
Get the latest AI workflows to boost your productivity and business performance, delivered weekly by expert consultants. Enjoy step-by-step guides, weekly Q&A sessions, and full access to our AI workflow archive.
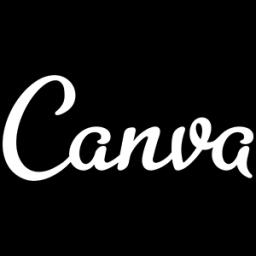
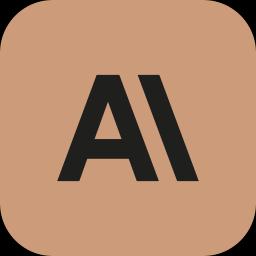
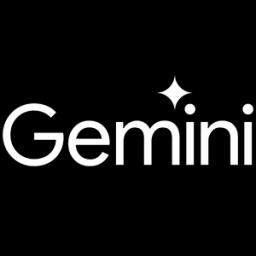
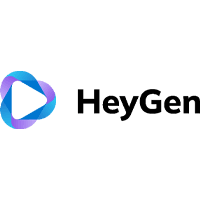
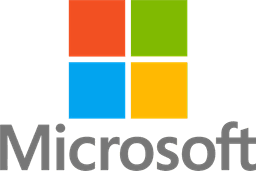
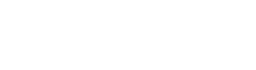
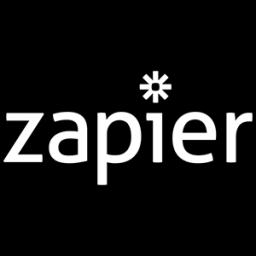
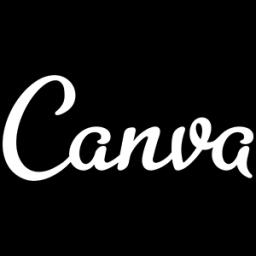
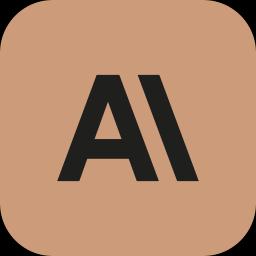
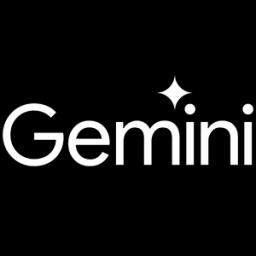
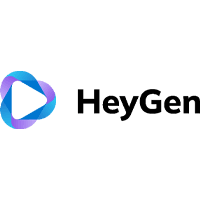
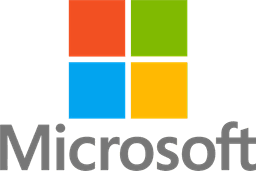
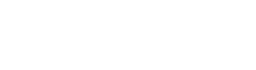
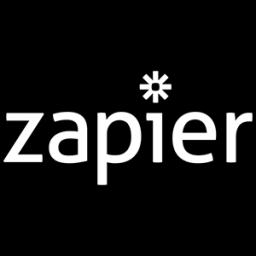
In conclusion, strategizing for the future of the manufacturing sector requires a collaborative effort between industry players and policymakers. Embracing IT consolidation, focusing on robust workforce development strategies, and implementing supportive policy frameworks are critical to overcoming the labor challenges and securing the sector's contribution to economic growth. As these recommendations are put into action, they promise not only to fill the labor gap but also to transform the industry's operational landscape, making it more adaptive, sustainable, and competitive in the coming years.